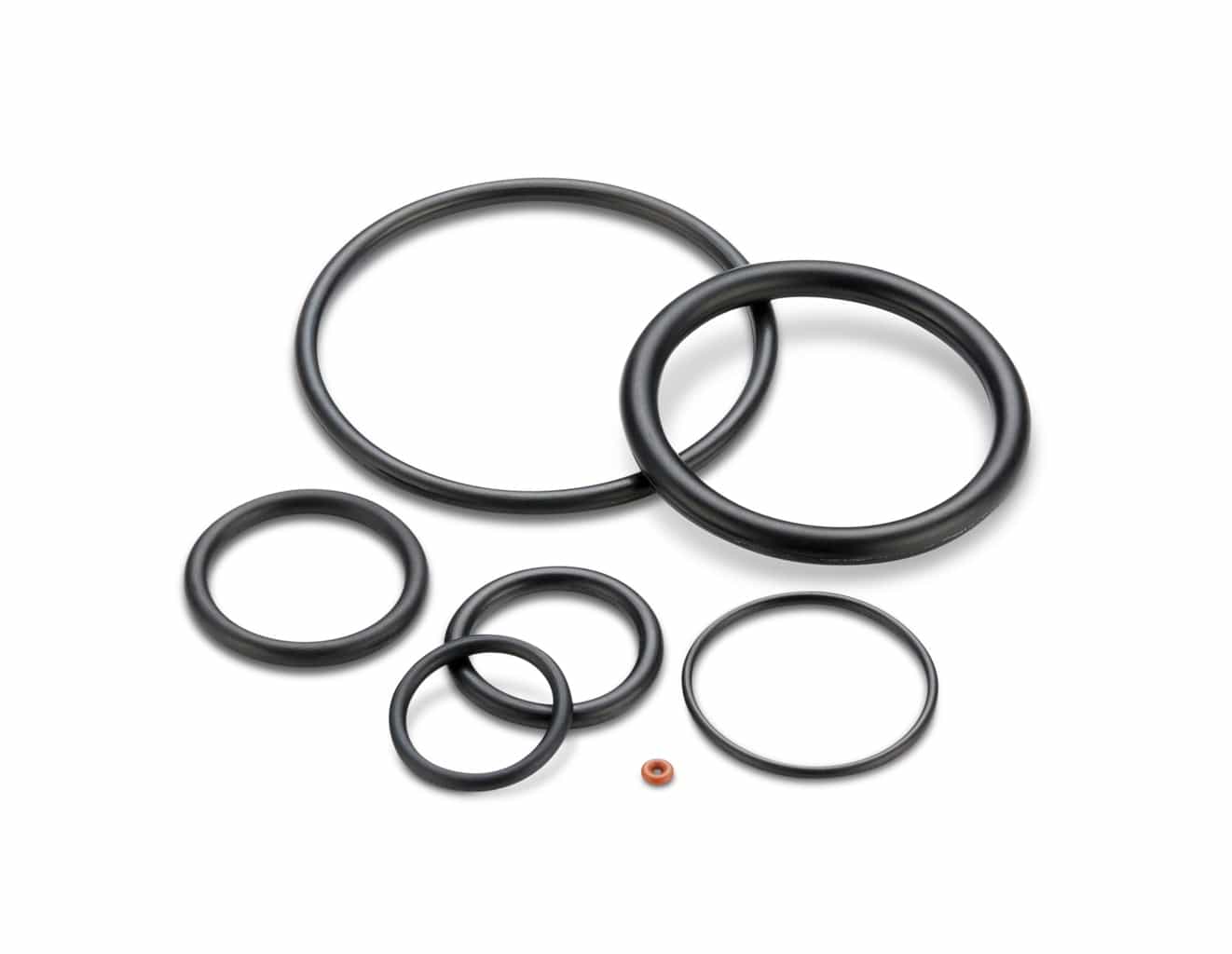
Sealing Systems Rotary Seal Application
Application description: Hydraulic Pump
- Shaft diameter 0.750″ ±0.001
- Bore diameter OD 0.753″ ±0.001
- 150 psi Hydraulic oil
- .103″ cross-section Quad-Ring® Brand seal
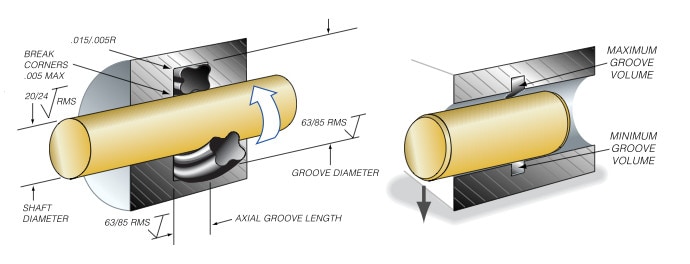
Ring Size | Cross-Section | Axial Groove Width “D” +0.005/-0.000 |
---|---|---|
Q4102 – Q4178 | 0.103 ±0.003 | 0.110 |
1. Calculate groove dimensions
Groove Diameter = Minimum Shaft Diameter + (2 x Min Cross-Section) – 0.004″
Groove Diameter = 0.749 + (2 x 0.100) – 0.004
Groove Diameter = 0.945 in ±0.001
2. Groove width = 0.110″ -0.000/+0.005
3. Calculate Minimum Groove Volume
Minimum Groove Volume = ((Min Groove Dia. – Max. Bore Dia.)/2) x Groove Width
Minimum Groove Volume = ((0.944 – 0.754)/2) x 0.115
Minimum Groove Volume = 0.0109 in2
4. Calculate Maximum Quad-Ring® Brand Seal Volume
Maximum Quad-Ring® Brand Volume = (Maximum Cross-Section)2 x 0.8215
Maximum Quad-Ring® Brand Volume = 0.1062 x 0.8215
Maximum Quad-Ring® Brand Volume = 0.0092 in2
5. Compare Minimum Groove Volume to Maximum Ring Volume
In this application the Maximum Ring Volume is less than the Minimum Groove Volume; everything appears to be OK.
6. Calculate Minimum and Maximum Seal Squeeze
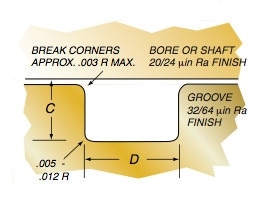
These calculations look at both ends of the worst-case stack up
tolerance, including rod shift, to determine the maximum and
minimum ring squeeze.
Maximum Seal Squeeze =
- 1 – (Minimum Groove Depth / Maximum Ring Cross-Section)
- Minimum Groove Depth = (Minimum Groove diameter – Maximum Bore)/2
- Minimum Groove Depth = (0.944 – 0.754)/2
- Minimum Groove Depth = 0.095
- Maximum Seal Squeeze = 1 – (0.095 / 0.106)
- Maximum Seal Squeeze = 10.3%
- Minimum Seal Squeeze = 1 – (Maximum Groove Depth / Minimum Ring Cross-Section)
- Maximum Groove Depth = ((Max. Groove Diameter. –
- Max Bore)/2) + (Max Bore – Min. Rod)
- Maximum Groove Depth = ((0.946 – 0.754)/2) + (0.754 – 0.749)
- Maximum Groove Depth = 0.096 + 0.005
- Maximum Groove Depth = 0.101
- Minimum Seal Squeeze = 1 – (0.101 / 0.100)
- Minimum Seal Squeeze = -1.0%
In this application, if every dimension went to the worst side of
the tolerance and the piston was side loaded, the seal would leak. To avoid these problems:
1. Reduce the clearance between the bore and piston.
2. Reduce the tolerances of the bore and piston.
3. Use a larger cross section Quad-Ring® Brand seal to absorb the extra tolerance.
4. Support the piston so that it can not move off center.
7. Calculate Maximum Clearance and Evaluate Possible Extrusion Issues
- Maximum Clearance = Maximum Bore – Minimum Rod
- Maximum Clearance = 0.754 – 0.749
- Maximum Clearance = 0.005″ (0.0025″ Radial)
This application has a max clearance of 0.0025″ and must withstand 150 PSI without extruding the Quad-Ring® Brand seal. Refer to the clearance chart. A 70 Shore A material at 150 PSI can withstand a maximum clearance of 0.009, so a 70 Shore A material will work. Making improvements to the Minimum Seal Squeeze issues in Step 6 will also reduce any possible issues with seal extrusion.
8. Select seal size
For all rotary rod seal applications select a Quad-Ring® Brand seal that has an ID larger than the maximum shaft diameter.
Part ID >= 0.751″
Quad-Ring® Brand Seal Size = 4117