
Case Study
Tailoring Drug Delivery and Storage Systems to Meet the Evolving Market
Pushing design boundaries with materials science to respond to the voice of the patient
Challenge
Develop solutions in the medical device/pharmaceutical industry for inconspicuous wearable drug delivery technologies
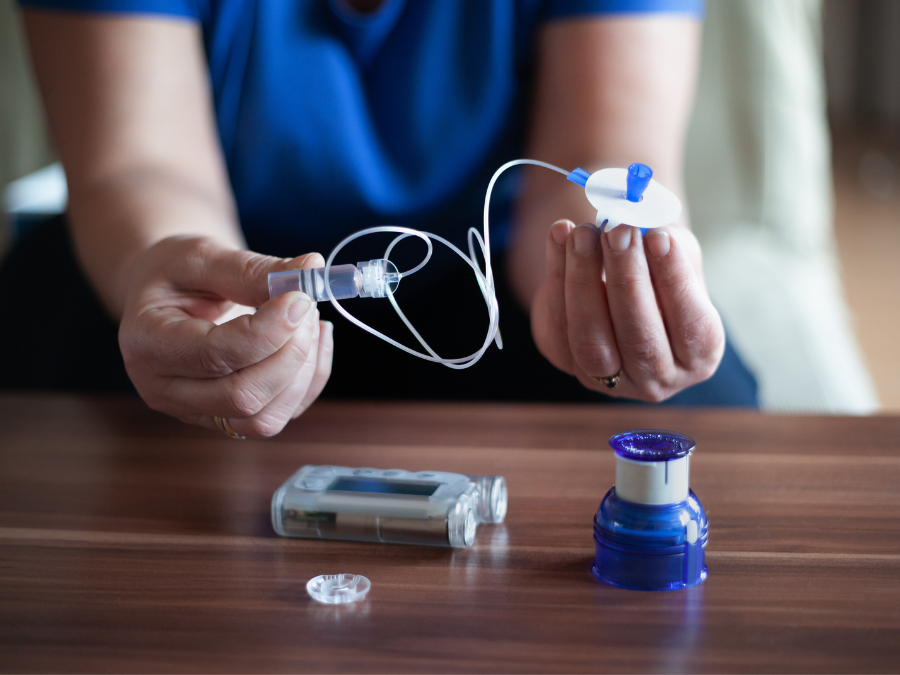
There’s a need in the medical and pharmaceutical industries for tailored drug delivery and storage systems that accommodate patient requests for discreet wearable technologies allowing them to conduct a normal lifestyle. Current products and/or solutions are inadequate; The challenge is twofold:
- Application environments are challenging for current industry material properties and capabilities
- The drug delivery devices don’t meet the lifestyle demands of the device users
The wearable industry continues to expand, driving demand for smaller device sizes of existing applications and developing new applications to deliver drug products.
Manufacturing Considerations & Challenges:
- Aggressive packaging and delivery needs
- Sterilization methods, and varying compliance use-cases and conditions, including chemical and environmental interactions
- Storage requirements for new treatments
For example, in cancer therapy and cell harvesting technologies, packaging and storage systems must weather extreme conditions while maintaining high performance levels. Solution providers with materials science as a key capability can lead the way with new material formulation offerings that push boundaries once considered impossible.
Solutions
Three mainstays for providing a drug delivery and packaging solution for our customers:
Material: Our Advanced Materials Group immediately begins evaluating the best material for application suitability, compatibility with the drug, chemistry or environment and biocompatibility with the human body. The ideal environment is a storage or delivery system that has zero interaction with the chemistry that it is in contact with. This is often impractical, so the typical objective is to develop “CLEAN” material solutions to mitigate the risk of adverse material interactions with the chemistry. The component within the application must not alter the drug, so it performs as it should.
Design: In parallel, our design team discusses the device mechanics, asking, “What does it need to do, and how well does it need to do it?”. Drug delivery and packaging systems often require aggressive packaging and delivery solutions, and the range of storage requirements can be significant. Using a Design-for-Manufacturing (DFM) approach, our experts collect the customer’s input and incorporate it into the design. Our ability to use Finite Element Analysis (FEA), Mold Flow Analysis (MFA) and Failure Modes and Effects Analysis (FMEA) provide an analytical approach for identifying and resolving potential application failures. An optimal design considers safety, cost, performance, quality and reliability.

Regulatory: We support our customers with testing and documentation that enables them to comply with FDA and EU regulations. This critical step must consider the specific environmental, biocompatibility and regulatory standards that comply with Current Good Manufacturing Practice (CGMP) regulations. The drug delivery system will be challenged through a series of biocompatibility tests that may include ISO 10993, USP Class VI and other testing such as leachate and extraction to ensure the chemistry of the drug is unaltered by the storage/delivery system. We often perform cytotoxicity testing as this is the most cost and time efficient test and is applicable to the greatest number of industry applications. In addition, we manage the testing of irritation and sensitivity, acute systemic toxicity and hemocompatibility.
About Us
Our Engineers Are Eager to Help You Solve Your Toughest Elastomer + Thermoplastic Challenges
Minnesota Rubber and Plastics is a world leader in the material compound development, engineering design and manufacturing of custom molded elastomer and thermoplastic components and assemblies. For over 75 years, our engineers have collaborated with world-class organizations to help solve difficult sealing and component challenges, earning us the global reputation for producing “the tough parts”. Customers have direct access to our engineers and technical experts. The result: Fast, detailed answers that solve design and manufacturing challenges Your team will have direct access to our engineers + technical experts.
Our Collaborative Innovation Process, Under One Roof
Our collaborative innovation process fuels innovation and shortens development times. Involve us early in your design process and our immersive collaboration approach can open new doors and explore solutions that improve the performance and value of your products. Minnesota Rubber & Plastics offers a full spectrum of materials — including rubber, silicones and thermoplastics — which can be customized to your exact specifications. Explore our immersive design-prototype-build-test process that can be uniquely executed under one roof in our new innovation center to get your differentiated product to market faster than ever.
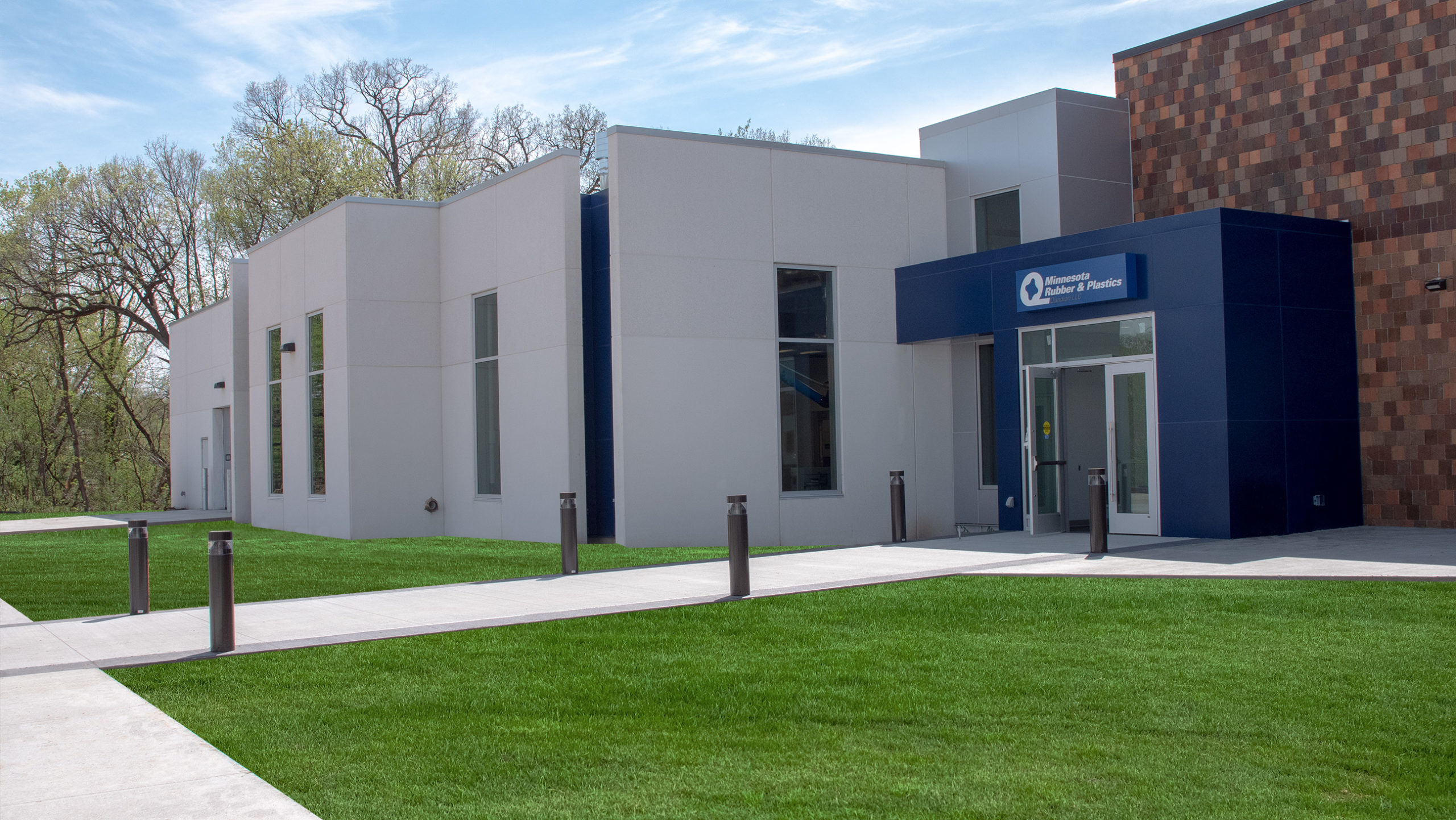
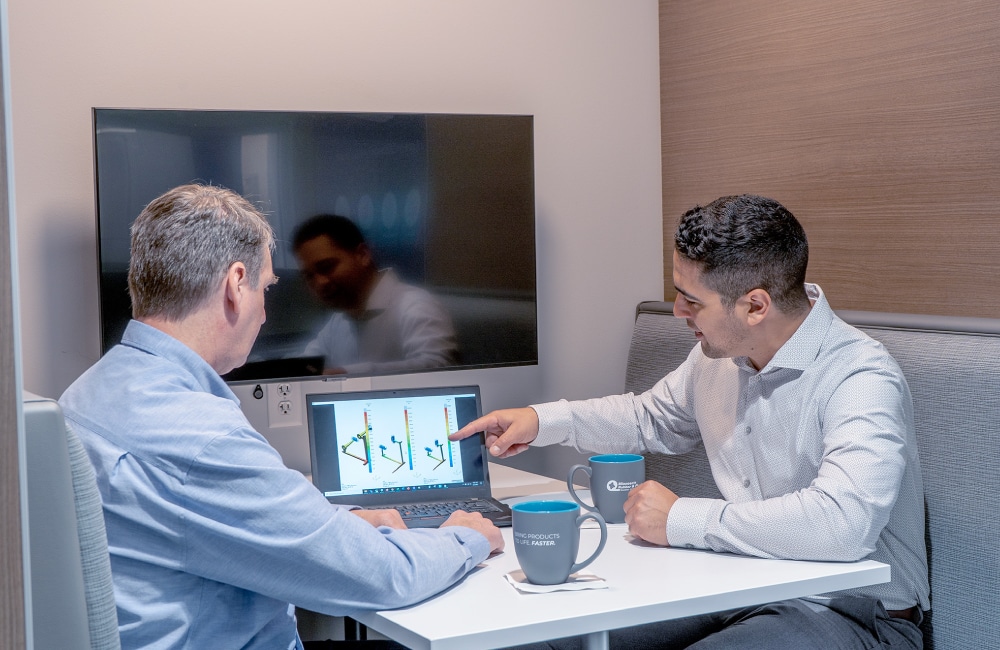
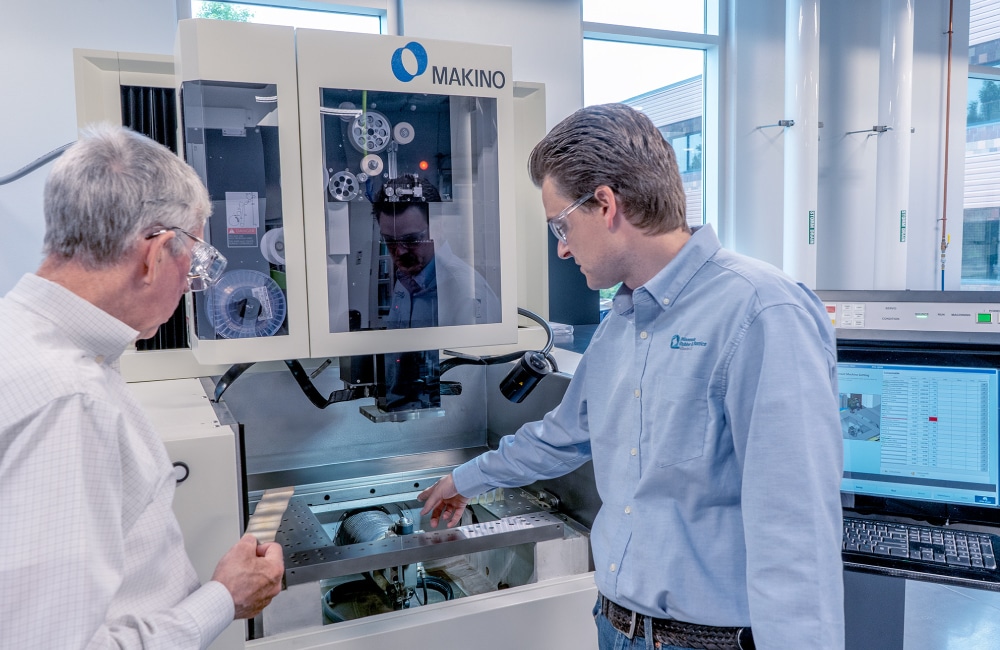
Comprehensive Engineering and Manufacturing Capabilities
Minnesota Rubber & Plastics specializes in formulating, designing, manufacturing and assembling rubber, silicone and high-performance thermoplastics for discerning customers.
Examples of our services include:
- Mechanical design and DFM review
- Materials analysis; specialty elastomer compounds
- Metal-to-plastic and plastic-to-plastic conversions
- FEA and mold-flow analysis
- Laser marking and pad printing
- Ultrasonic welding
- Functional and leak testing
- Fully equipped Advanced Materials Lab including:
- Infrared Spectrometer (FTIR)
- Infrared Microscope
- Differential Scanning Calorimetry (DSC)
- Thermogravimetric Analysis (TGA)
- Rubber Process Analyzer (RPA)
- Moving Die Rheometer (MDR)
- UV-Vis Spectrophotometer