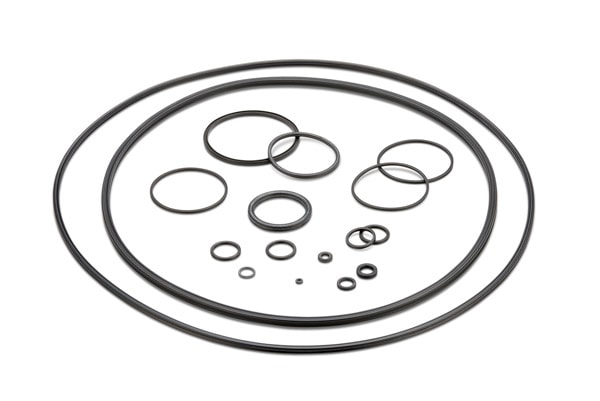
Selecting an Elastomeric Material
One of the most important aspects of designing a sealing system, or any other elastomeric component, is making a proper material selection.
There are many different elastomeric materials from which to choose, and selecting the “best” material means balancing suitability for the application, performance, cost, and ease of manufacturing.
Minnesota Rubber & Plastics manufactures and uses hundreds of different types of elastomeric materials. Answers to these common questions will help direct you towards the appropriate material type(s) to consider in your application.
- How and where will the part actually be used? How will it be stored and transported? What will it be located next to?
- What is the environment in which the seal or part is operating, including fluids, gases, contaminants, pressures, temperatures, etc.?
- What are your performance objectives for the part, including life span and duty cycle?
- What is your product worth in the marketplace, and are your performance objectives achievable at the market price?
When selecting a material for your application, consider the following:
- The primary fluid(s) to which the elastomer will be exposed.
- Secondary fluids to which the elastomer will be exposed, such as cleaning fluids or lubricants.
- Exposure to chloramines in water.
- The suitability of the material for the application’s temperature extremes, both hot and cold.
- The presence of abrasive external contaminants.
- The presence of ozone from natural and artificial sources, such as electric motors, which can attack rubber.
- Exposure to processes such as sterilization by gas, autoclaving, or radiation.
- Exposure to ultraviolet light and sunlight, which can decompose rubber.
- The potential for outgassing in vacuum applications.
- Will the product come in contact with the human body, directly or indirectly, and if so, for how long a period?
- Does your part need to be a special or specific color?
Contact us for assistance with selecting a material for your application.