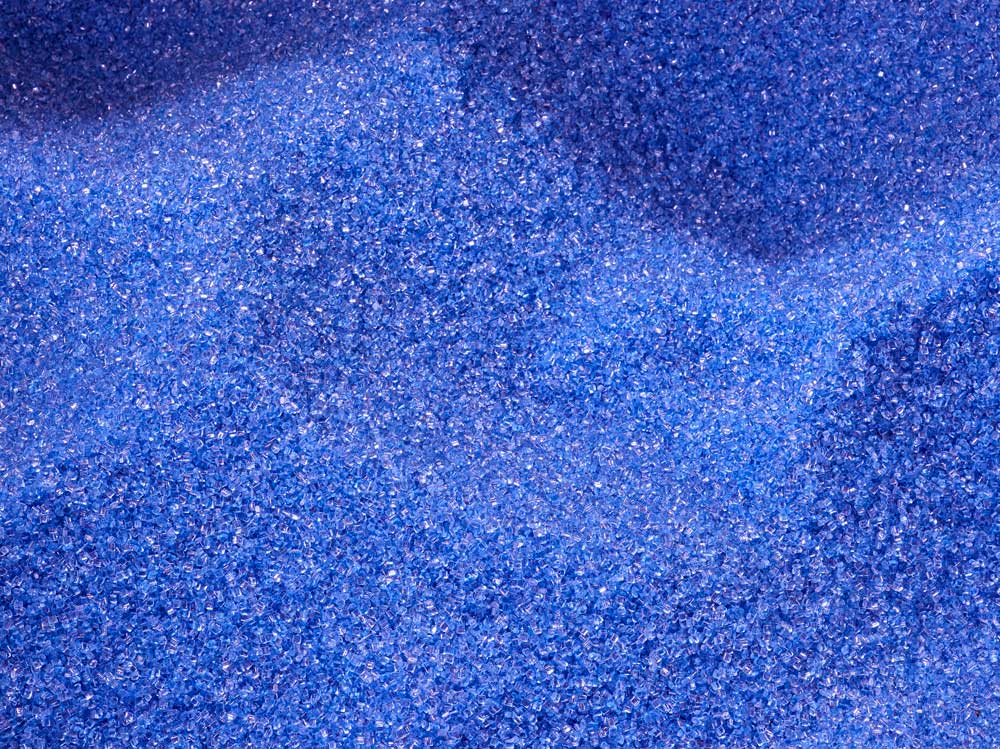
Structure of Thermoset Plastics vs Thermoplastics
When classified by chemical structure, there are two generally recognized classes of plastic materials: Thermosets, having cross-linked molecular chains, and Thermoplastics, which are made up of linear molecular chains.
Thermoset polymers require a two-stage polymerization process. The first is done by the material supplier, which results in a linear chain polymer with partially reacted portions. The second is done by the molder, who controls final cross-linking. Short chains with many cross-links form rigid thermosets, while longer chains with fewer cross-links form more flexible thermosets. With all thermosets, the polymerization is permanent and irreversible.
Thermoplastic polymers require no further chemical processing before molding. There are two types of thermoplastic polymers: Crystalline and Amorphous. The pyramid graphic located here identifies many of our common thermoplastic materials.
Crystalline Polymers
- Have a relatively sharp melting point.
- Have an ordered arrangement of molecule chains.
- Generally require higher temperatures to flow well when compared to Amorphous.
- Reinforcement with fibers increases the load-bearing capabilities considerably.
- Shrink more than Amorphous, causing a greater tendency for warpage.
- Fiber reinforcement significantly decreases warpage.
- Usually produce opaque parts due to their molecular structure.
Amorphous Polymers:
- Have no true melting point and soften gradually.
- Have a random orientation of molecules; chains can lie in any direction.
- Do not flow as easily in a mold as Crystalline Polymers.
- Shrink less than Crystalline Polymers.
- Generally yield transparent, water-clear parts.
Long Glass and Short Glass
How long is long?
Long glass is typically 11mm long x 0.3mm in diameter. Normally the glass fibers lay parallel within the strand.
Short glass is usually 3mm long x 0.3mm in diameter.
Normally when we make reference to “Glass Filled” we are referring to short glass unless otherwise specified.